Coal handling
Coal is lifted from the hold of the ships by the grippers on the bridges or the derrick, respectively. The coal can then be dropped directly onto the storage areas (2 storage areas, A and B), or, which is the normal way of doing it, into a bunker, from which it is transported via several conveyor belts to the storage areas. The last conveyor belt (the discharge conveyor) has reversible movement direction, so that both storage areas, which are separated by a section of track, can be served. It is also traversable on the box girder, with the whole box girder swivelling, so that every place in the storage areas can be reached. The height of the whole girder is also hydraulically adjustable.
The problem
Depending on the type of coal, its country of origin and the weather, its handling generates dust. The largest source of this dust is due to the height adjustability of the discharge conveyors.
If the space between the conical pile and the discharge belt is too large, the result is large amounts of dust. An easterly wind carries this dust towards a neighbouring city. The first residential buildings are located only a few hundred metres from the facility and are thus affected by the dust. That resulted in many complaints by the residents which led to endeavours to curb these amounts of dust.
To exclude the human factor, the aim was to achieve an automatic height adjustability of the discharge conveyors, which would ensure that the height the coal is discharged at is as low as possible at any given time to keep the dust at a minimum.
The solution
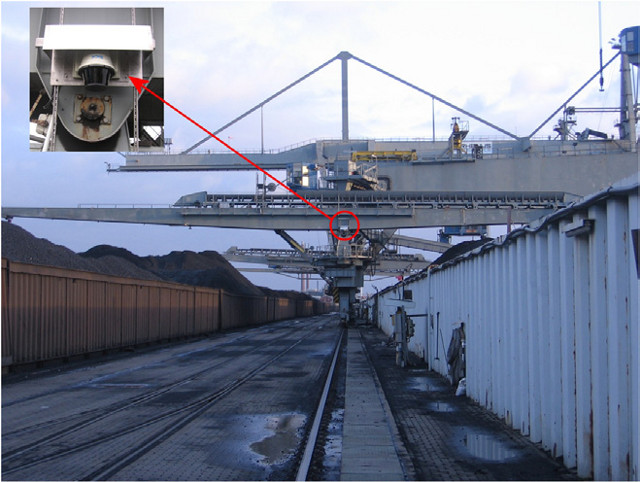
Since the box girder of the discharge conveyors is height adjustable and swivelling, and the conveyor is traversable on the girder, it was a particular challenge to find a sensor technology which allows us to determine - at any position - the distance between the conical pile and the discharge conveyor.
To achieve this, a laser scanner developed by Sick was used. With the assistance of a laser on a level with adjustable angles, it measures the distance to objects on this level. It is able to cover an area of ca. 330 degrees.
The scanner is centrally attached to the girder of the discharge conveyor, below the axis of rotation of the hoist. From there, the coal discharge onto both storage areas can be observed. The scan level is right below the box girder. The swivelling does not cause any problems as the scanner also swivels at the desired assembly position.
The traverse of the conveyor is compensated by the measuring of its vertical movement. A linear encoder is employed, also developed by Sick. Since the laser scanner calculates the distance to every object on the scan level, the objects below the discharge position can be targeted accordingly. The tilt angle of the discharge conveyor is determined with an inclinometer and regulated according to the calculated data.
Additional benefits
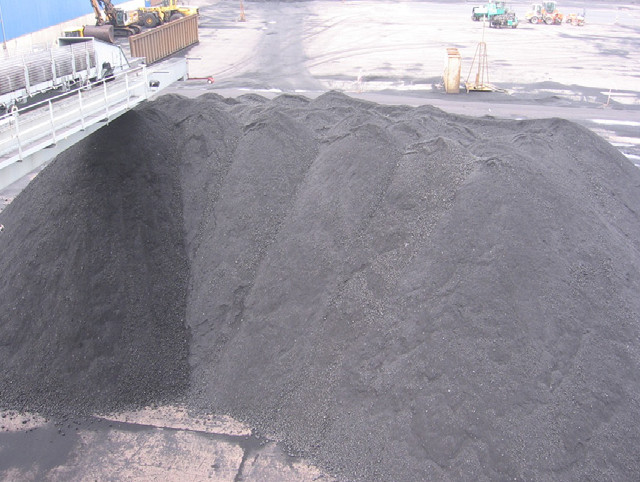
In addition to regulating the discharge height, an automatic stocking of the storage areas has become possible. Fully automated, the coal can now be spread evenly on the storage area utilizing the height adjustment, the automatic swivelling and the travel of the discharge conveyor on the box girder.
The controls
The controls of the laser scanner, the evaluation of the measured data and the handling of communication have been implemented with a Siemens S7-300 PLC. Communication takes place via Ethernet. The controls have been seamlessly integrated into existing elements.
Why HIT?
HIT has implemented the automation of coal drop lines to the full satisfaction of the operators and has been supervising this facility since it was completed. The facility proved its reliability from the very beginning. The dust emissions have been significantly reduced by the height adjustability, so that the handling of the coal is also possible when the wind comes from an easterly direction without any inconvenience to the residents.