The process
The automated manufacture of concrete sleepers starts in the loading station with the pressure-monitored loading of pre-stressing steel in a frame. This is placed in a special mould which is then filled with concrete. After the concrete has been vibrated, a ‘lid’ is placed on the mould, the frame is rotated by 180 degrees and put down. The mould is then swung back so that the sleepers are demoulded. These concrete sleepers, which are still in the frame, are automatically moved to the hardening warehouse with the stack crane. After the continuous hardening process is over, the concrete sleepers are then removed from the warehouse fully automatically using a second crane and then undergo the final treatment.
The empty frames are transported back to the loading station using hoisting gear and conveyor belts, thus completing the production cycle.
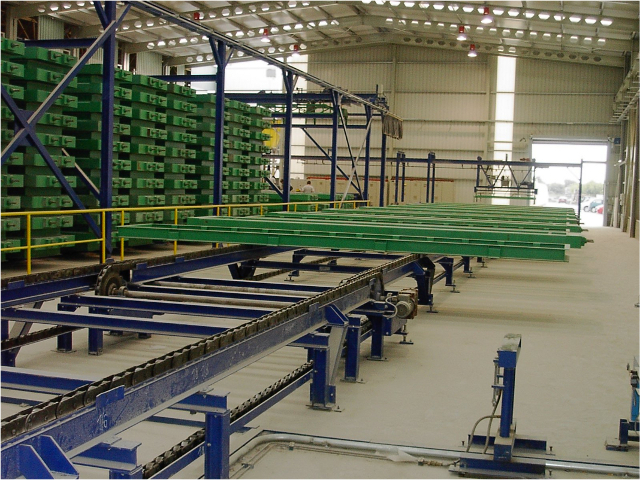
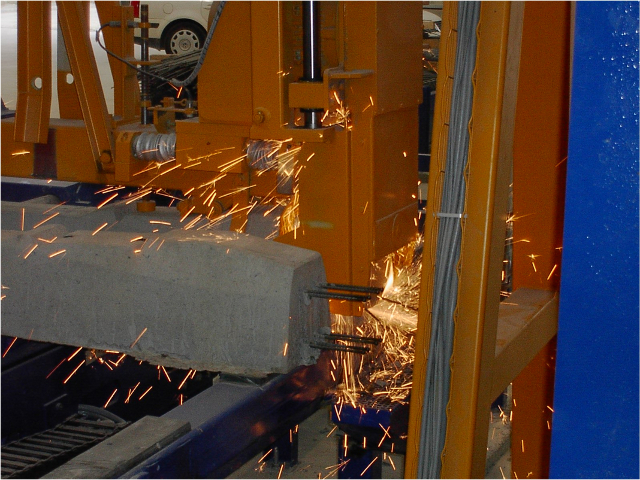
Warehouse management system
A fully automatic warehouse management system with two gantry cranes ensures that the finished railway sleepers are transported to the correct storage areas and are not released for removal from the warehouse until the hardening time is over. Space cleared by removing sleepers from the warehouse is automatically reassigned to ensure optimal exploitation of the available storage area. The number of railway sleepers in the warehouse can be called up at any time.
The controls
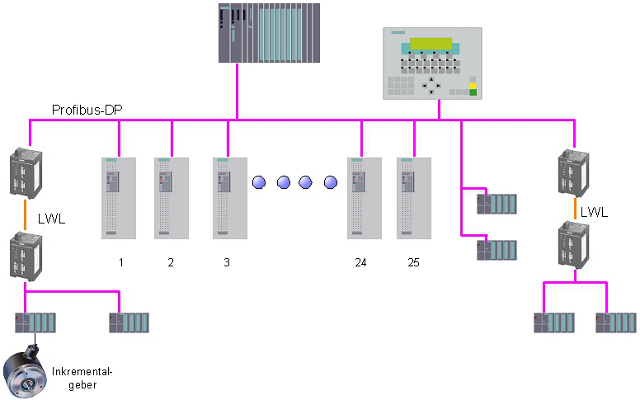
The system is designed so that it can operate fully automatically and in manual mode. The core of the control system is a Siemens PLC type 414-3 DP. Via an extensive optical waveguide Profibus field network, it is connected to the individual onsite control cabinets as well as to the position encoders, the pressure measuring units and the frequency converters. A large number of drives are supplied via a total of 25 frequency converters. If needed and at their request, we can provide the company with service support in a very short time via modem link.
Why HIT?
HIT has implemented this project to the full satisfaction of our client and has maintained the system since it was set up in 2004. From the very beginning, the system proved its reliability. In addition, it was possible to increase the production of railway sleepers through a professional optimisation of the processes.