Project description: Transferring of data to superordinate systems
The design of the mixer has been technologically updated by using Siemens type S7-300 controls. The PLC- programs designed by us have been structured in a way that allows them to be utilitized in a more flexible manner for different types of mixers. All of the recipe administration has been realized in the controls.
The data can be amended, modified and secured not only on a docked PC, but also on the operating panel OP17. Additionally, product and history can be transferred to the PC. Depending on the client’s wishes, an Excel-application or a WinCC-application (including the option user-archive) can be installed. The additional exchange of data with an inventory control system is, of course, also possible.
Communication
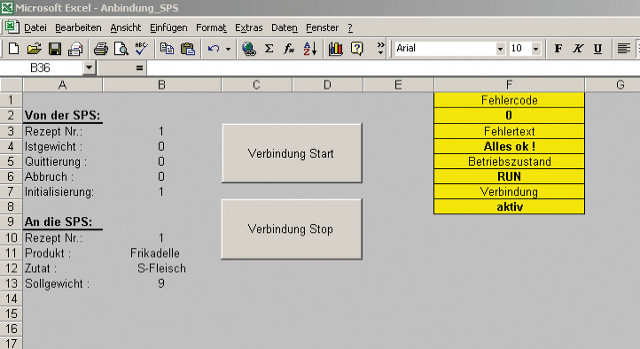
The mixer controls are connected via the MPI interface with the superordinate system (here Excel or WinCC). All data relevant to the products can be transferred from the superordinate system to the controls, or back from the controls. Furthermore, current process data is recorded and secured in the superordinate system as history data. The recording of actual data ensures a full verification of the product quality.
Operation
With a user-controlled operation on the basis of operating panel OP17, all functions of the machine can be accessed. Additionally, displays of all machine data are provided. The operation allows a flexible parameterization of the automatic functions, the starting and stopping of the work processes and the automatic functions, as well as the recipe administration.
Option WinCC
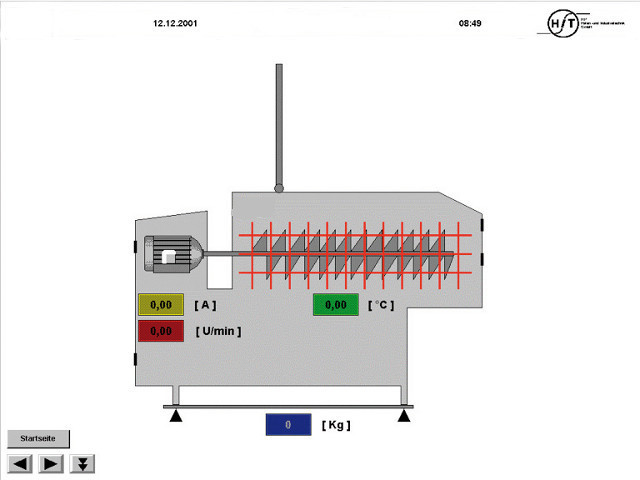
Optionally, the operation can be achieved by WinCC, a Siemens product. The opening and closing of doors is signalled graphically. Current machine data, such as power consumption, temperature, weight and operating states of the machine are shown on the visualization images and recorded simultaneously. The recording and visualization of temperature charts, current patterns etc., is part of the system just like the graphic signalling of error messages. All alert messages are recorded in a history file and can be called up at a later date.
Why HIT?
HIT have successfully completed the modification of a mixer control system with integrated visualisation. From the very beginning the system has shown its reliability. Through the design of a flexible control program, this software can be adapted in the shortest possible time to different machine configurations. The commissioning times have been reduced considerably.