Project description
Gas is transported to consumers via an extensive gas-pipe network. This network is supplied by booster stations, some of which are located on the East Frisian coast in northern Germany and supplied with gas from North Sea drilling platforms. The gas pressure is between 85 and 130 bar. Before this gas can be supplied to the individual municipal networks, the gas pressure is reduced to approximately 35 bar using gas pressure regulator systems situated on the outskirts of the towns. The expansion of the gas results in a cooling of the medium. Both, the pressure and the temperature regulation, have been realized using the process control system PCS7. In addition, a large number of process signals are registered.
In total three systems located just outside the city of Bremen have been automated. These systems are operated centrally by Bremen’s municipal works from a control room outside the city. Data is transferred via a dedicated line. In addition to the central operation, onsite operation is also possible.
The controls
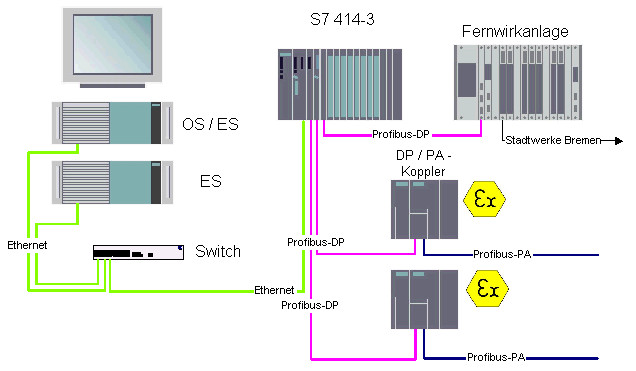
The PCS7 system consists of two redundant visualisation PCs, which are connected to the controller S7-400, CPU 414-3, via an “Industrial Ethernet”.
The controller in turn is connected by a Profibus-DP – and a Profibus PA – system to the sensors and actuators in the field or the external area respectively. This design provides a clear system structure. The control and visualisation system has been modularly “engineered from top to bottom” with PCS7.
This procedure has created a coherent control level with a clearly structured control program.
The program modules have been devised with the aid of the CFC programming system so that complex functions are displayed in an uncomplicated manner.
Visualisation
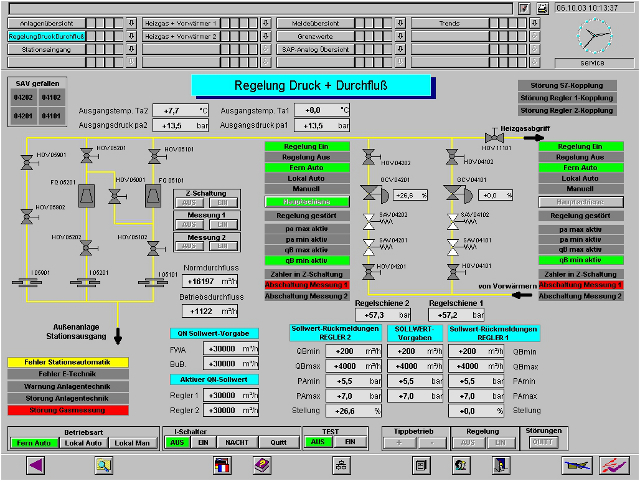
The visualisation provides an overview of the entire system at a glance.
The current states of the valves, pressure transducers, temperature sensors, flaps, slide valves and other units are indicated either by colour coding or by setpoint and actual values being displayed.
Essential information, which is available in the controller, is registered, processed and archived in the PC7 database. The archived data include temperature and pressure curves as well as error and status messages.
Why HIT?
HIT successfully completed this project. A clear user interface was de¬signed for the operators and a good system and software structure was created for the service team. From the very beginning, the system proved its reliability. These features have increased the failsafe performance and the productivity of the system.