Glas Wool Defibering Machines for producing insulating wool
Defibering machines form the heart of factories producing insulating wool. Similar to the way candyfloss is made, a centrifugal process causes liquid glass to be forced through a large number of minute boreholes at the edge of a centrifugal disc, exiting the disc as a fibre. These fibres are drawn by an air current from an air ring fitted under the disc. As wool, the insulating material drops down into a chute onto a conveyor belt.
A ring-shaped burner is used to heat the disc; this is fired with an air/gas mixture and has a heat output of several hundred kW.
The performance of the burner has a direct effect on product quality in this process. For this reason, it is important for the heat output and the flame pattern to be metered extremely accurately, for regulation to be carried out with a high precision performance and for the machine settings to represent a reproducible dependency between its settings and its flame pattern
In each of the plants, between four and nine systems are operating in parallel to achieve the required production quantities.
The controls
Using cascaded control circuits, the heat output and the flame pattern are metered and regulated accurately to achieve a reproducible fibre quality. Various parameters such as the quantity of air, gas, glass and air ring air, residual oxygen content in the waste air, disc rotational speed and so on, serve as controlled variables.
The control circuits are implemented with powerful CPUs from the controller types Simatic S5–135U or S7–400.
These controllers are connected via Profi process field bus networks to the individual onsite control cabinets, the frequency converters and the powered actuators for the regulation of the nozzles.
On a higher level, process data is exchanged with the visualisation system WinCC via an H1 bus or Ethernet.
Monitoring by failsafe PLC
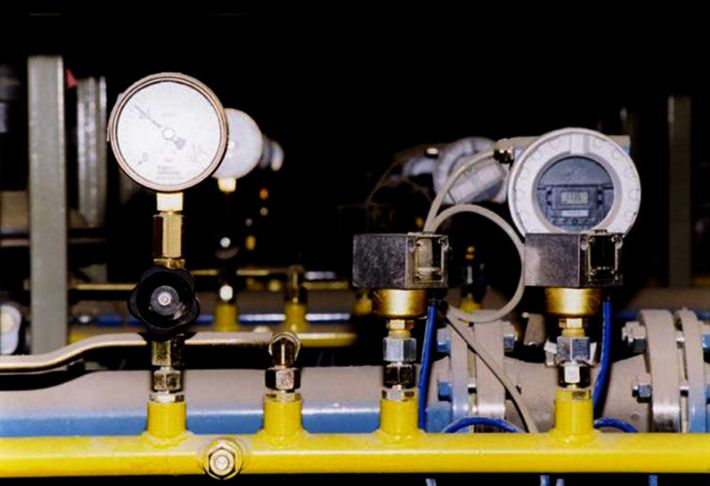
Another important criterion of these systems is the safety concept of the burners. Overriding safety functions are implemented with a failsafe PLC manufactured by Pilz PSS 3100. This PLC is connected via a Profibus DP to the Simatic controller and monitors all safety-critical functions and events.
The concept has been inspected and certified by the TÜV Rheinland.
Why HIT?
HIT has implemented these projects to the full satisfaction and has maintained the system since it was set up. From the very beginning, the systems proved their reliability. Through the high precision performance, it was possible to improve the product quality and a safety standard has been achieved that previously did not exist in this line of work.