Container gantry
The container gantry was comprehensively modernised, including the control technology and the safety technology. The container gantry is equipped with a hoist, a boomhoist, a hoist trolley and a running gear. It reaches a lifting height of c.40m and a maximum capacity load of c.60t. The delicate execution of individual crane movements, its reliability as well as its robustness are important features of the container gantry.
Project description
The old controls as well as the old converters were replaced by the new S7 controls and new converters type Siemens Sinamics DCM. The general control system of the crane was retained. The switch cabinets for the low voltage electronics, the PLC controls, the power electronics of the hoisting unit, the running gear, the hoist trolley and the boomhoist drives were newly developed, delivered and installed in the E-house. Analogue displays were built into the respective switch cabinet flaps which display the respective field voltage and field current as well as the armature voltage and armature currents. The old analogue speedometer of the hoisting unit, the boomhoist and the crane running gears were replaced by the enco-der system U-ONE by Hübner Giessen. The control seat and the control panel in the driver’s cabin were replaced by a new control seat. The functionality was not affected. This facilitates the directing of the crane drivers to the modified container gantry.
Visualisation
The visualization was created using the Crane Management System (CMS) by Siemens. The visualization enables an overview of the complete container gantry.
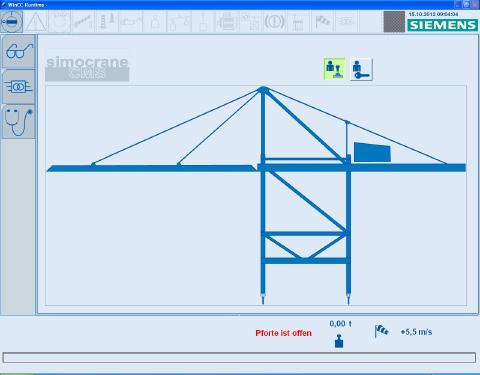
Current conditions, like wind speed, limit switch positions and error archive are presented clearly. These are available to the crane driver at any time. Additionally, all information is transmitted to the central exchange so that any errors can be acted upon at any time.
Monitoring via failsafe PLC
Another important characteristic of this facility is the safety concept. The PLC is a failsafe S7-317F by Siemens. All functions relevant to the safety, such as emergency stop signals, emergency limit switches, overload signals etc., are conducted on failsafe entry points or exit points respectively
Improving the energy balance
The container gantry can not only save energy costs with its more efficient and highly intelligent components, but can also improve the CO2 footprint. Running gear motors with a higher degree of efficiency, an adapted compensation system and LED lighting were installed, amongst others.
Another special feature that needs to be mentioned is the air-conditioning of the E-house. This occurs at a low outside temperature through a passive ventilation of the E-room. At high outside temperatures there is a switch to an active air-conditioning unit.
Why HIT?
HIT have successfully completed this modernization. A clear user interface was designed for the operators. From the very beginning, this container gantry has proved its reliability. These features have increased the failsafe performance and the productivity of the system.