Modernisation of a Production Line for Snacks
The previous automation technology of this line consisted of multiple individual controls. These were partly conventional relais controls as well as electronic regulating and control modules. The individual controls were not interconnected or hardly connected at all. It was not possible either to display and operate the complete line in the previous visualization system.
The modernisation included the integration of the individual control units in the existing controls as well as the extension of the visualization system for the operation and observation of the complete production line. For that, the existing Siemens controls were replaced by modern and high-performance Siemens controls with modern interfaces. To integrate the sensors of the old controls, these were connected in a decentralized way. The present “hardware regulators” were replaced by “software regulators”. For the dosage of flour and water, the existing dosage control system was replaced by the weighing module Siwarex FTC.
The existing PC-based operating and observation system InTouch was converted to the most recent version and expanded to include the renewed components. A recipe administration and data archive round off the operating of the whole production.
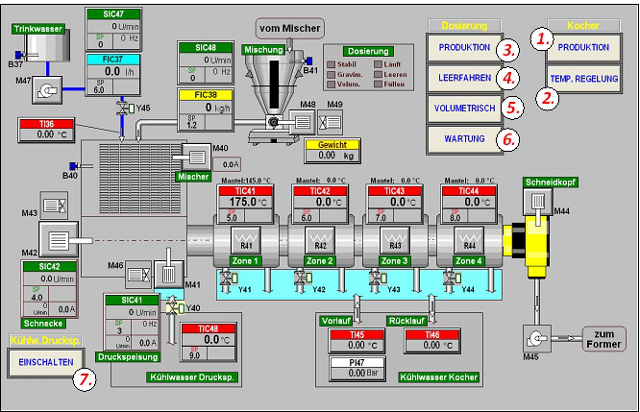
Process description
The production of pellets takes place in several steps. The part of the system described here (line 8) processes a finished dry mix into so-called pellets, which are then processed to become the finished snacks. The weighing and composition of the dry mix occurs in a centralized mixing system, and reaches the production line through a connecting pipe.
he incoming dry mix is dosed in a blender and moisturized with water. The moisturized mix is then pressure fed into a boil cylinder. The mixture is transported with a worm gear unit through several temperature zones to the outlet of the cylinder. The different temperature zones in the cylinder ensure the high-pressure induction of the thermal energy into the product. At the end of this process, the heated mixture is chopped up by cutting blades and transported via blower fan to the subsequent mould-extruder.
The chopped-up pieces of dough reach a blender, from whose outlet the moisture is sucked away. The mould worm gear unit picks the dough up and transports it to the outlet of the cylinder. Depending on the product, the dough is shaped using cutting and painting tools into the desired shape and colour (food colouring). Conveyor blowers take the shaped dough into the drying area of the production line. The drying process consists of several steps and physically requires most of the space of the production line. After the drying, pellets are created out of the shaped dough. These are then cooled and transported for packaging.
The controls
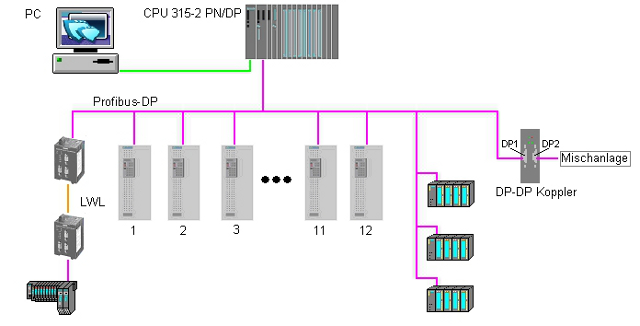
The visualization of the complete production line has been created using InTouch 10.1. The connection to the controls occurs via Ethernet. As controller a modern S7-300 CPU (315-2 PN/DP) is used. Via an extensive Profibus network, the decentralized assembly units and frequency inverter are connected to the controls.
Why HIT?
HIT have successfully completed this project. A clear user interface was designed for the operators, and a good system and software structure was created for the service team. From the very beginning, this system has proved its reliability. These features have increased the failsafe performance and the productivity of the system.