The recycling of PVC floor coverings starts with the collecting of the old previously removed coverings. These are cut into pieces and taken to the nearest collection point.
After sorting, the used PVC floor coverings are chopped up into chips of no more than 30 millimetres. After separating any metal bits with a magnet, a hammer mill gets rid of any adhesive screed and glue residue. After that, they are cleaned of these impurities by a screening machine. For the following fine grinding process, the PVC-material is cooled to a temperature of minus 40 C using liquid nitrogen. This cooling makes the PVC-chips brittle for a short period of time so that they can be ground into particles not exceeding 0.4 millimetres in diameter. This process is also described as Cryogen grinding.
The controls
During the second phase of modernization in 2009 a new controller system by Siemens was implemented. Because of the multitude of drives (51), the bus system SmartWire-Darwin by Moeller was employed.
The system can be operated fully automatically or manually. The measuring units located on the field, such as scales, flow metres, power sensors etc., are connected to the PLC via Profibus.
Visualisation with WinCC
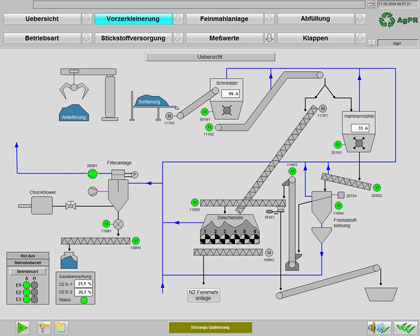
Two visualization platforms allow the system to be operated in the field and in the foreman’s office. Additionally, process data, such as temperature, material throughput and motor currents, are stored and can be displayed and printed out as tables or graphs.
Any important error messages are signalled acoustically until acknowledged. After they have been rectified, they are no longer indicated as “current errors” and archived.
Why HIT?
HIT has implemented this project to the full satisfaction of our client and has maintained the system since it was set up in 1994. From the very beginning, the system proved its reliability. In addition, it was possible to increase the material throughput to 150 % of the set point throughput by professionally optimising the control structures.