Kohleförderung
Die Kohle wird mit den Greifern der Umschlagsbrücken bzw. des Drehwippkrans aus den Laderäumen der Schiffe gehoben, welche die Kohle anliefern. Die Kohle kann dann entweder direkt auf die Lagerflächen (2 Lager A und B) geworfen werden oder, welches der normale Weg ist, in einen Bunker, von wo sie über mehrere Förderbänder zu den Lagerflächen transportiert wird. Beim letzten Förderband (das Abwurfband) ist die Laufrichtung reversibel, sodass beide Lager, welche durch einen Schienenstrang getrennt sind, beschickt werden können. Weiterhin ist es auf dem Kastenträger verfahrbar und der gesamte Kastenträger schwenkbar, damit jede Stelle auf den Lagerplätzen erreicht werden kann. Weiterhin ist die Höhe des gesamten Trägers hydraulisch veränderbar.
Problemstellung
Je nach Kohlesorte, Herkunftsland und Witterung kommt es bei der Förderung der Kohle zu mehr oder weniger starker Staubentwicklung. Die größte Gefahr der Staubentwicklung ergibt sich durch die Höhenverstellbarkeit der Abwurfbänder.
Ist der Abstand zwischen dem Schüttkegel der Kohle und dem Abwurfband zu groß, kommt es zu einer sehr starken Staubentwicklung. Bei Ostwind, wird dieser Staub dann in Richtung der Stadt getrieben. Die ersten Wohngebäude stehen nur wenige hundert Meter vom Gelände entfernt und werden von diesem Staub erreicht. Deshalb gab es viele Beschwerden der betroffenen Anwohner und damit schließlich das Bestreben, die Staubentwicklung einzudämmen.
Um den Faktor Mensch auszuschließen, war es das Ziel, eine automatische Höhenregelung der Abwurfbänder zu realisieren, damit gewährleistet ist, dass die Abwurfhöhe der Kohle jederzeit so gering wie möglich ist, um damit die Staubentwicklung weitgehendst zu reduzieren.
Die Lösung
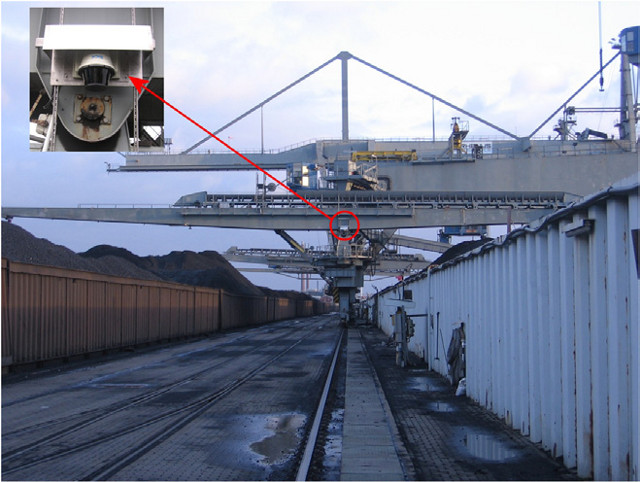
Da der Kastenträger des Abwurfbandes sowohl höhenverstell- als auch schwenkbar ist und das Band auf dem Träger verfahren werden kann, war es eine besondere Herausforderung eine Sensorik zu finden, die es jederzeit an beliebigerer Position zulässt, die Höhe zwischen Schüttkegel und Abwurfband zu ermitteln.
Zum Einsatz gekommen ist ein Rundum-Laserscanner der Firma Sick. Dieser misst mit Hilfe eines Lasers in einer Ebene mit einstellbaren Winkelschritten die Entfernung zu Objekten in dieser Ebene. Er ist in der Lage einen Bereich von ca. 330° abzudecken.
Der Scanner ist mittig am Träger des Abwurfbandes unterhalb der Drehachse des Hubwerkes befestigt. Von dort kann der Kohleabwurf beider Lagerplätze beobachtet werden. Die Scanebene liegt dabei kurz unterhalb des Kastenträgers. Das Schwenken macht keine Probleme, da der Scanner an der gewählten Montageposition mit schwenkt.
Das Verfahren des Bandes wird ausgeglichen, indem der Verfahrweg des Bandes gemessen wird. Dazu wird ein Linearencoder verwendet, der ebenfalls von der Firma Sick stammt. Da der Laserscanner zu jedem gemessenen Objekt in der Scanebene die Entfernung ermittelt, kann so gezielt auf die Objekte reagiert werden, welche sich unterhalb der Abwurfstelle befinden. Der Neigungswinkel des Abwurfbandes wird mit Hilfe eines Inclinometers bestimmt und anhand des gemessenen Wertes geregelt.
Zusatznutzen
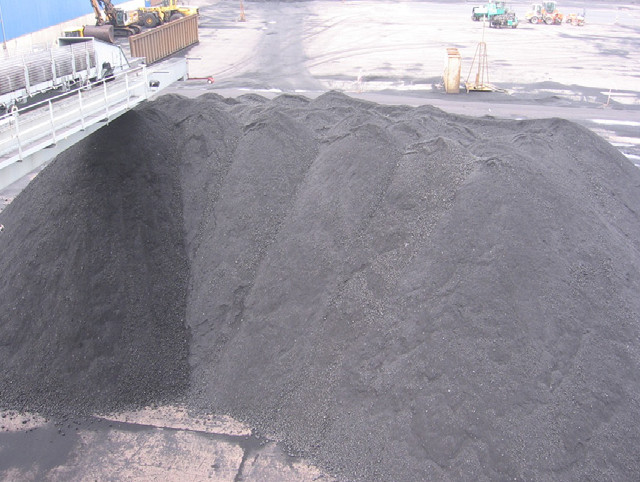
Zusätzlich zur Regelung der Abwurfhöhe ist nun auch die automatische Befüllung der Lagerplätze möglich. In der Vollautomatik wird die Kohle durch die Höhenregelung, automatisches Schwenken und Verfahren des Abwurfbandes auf dem Träger vollautomatisch gleichmäßig auf der Lagerfläche verteilt.
Die Steuerung
Die Steuerung des Laserscanners, die Auswertung der Messwerte und das Handling der Kommunikation wird jeweils mit einer Siemens S7-300 SPS realisiert. Die Kommunikation erfolgt über Ethernet. Die Bedienelemente wurden nahtlos in die bereits vorhandenen Elemente integriert.
Warum HIT?
HIT hat die Automatisierung von Kohleabwurfbändern zur vollsten Zufriedenheit der Betreiber realisiert und betreut die Anlage seit ihrer Erstellung. Von Beginn an hat die Anlage ihre Zuverlässigkeit bewiesen. Durch die Höhenregelung wird die Staubentwicklung stark reduziert, sodass ein Kohleumschlag auch bei Ostwind möglich ist ohne Anwohner zu belästigen.