Modernisierung einer Fertigungslinie für Schinkenchips
Die bisherige Automatisierungstechnik der Linie bestand aus mehreren einzelnen Steuerungen. Dabei handelte es sich zum Teil um konventionelle Relaissteuerungen als auch um elektronische Regel- bzw. Steuerungsmodule. Die einzelnen Steuerungen waren nicht oder nur unzureichend miteinander verbunden. Ebenfalls war es nicht möglich die komplette Linie im bestehenden Visualisierungssystem anzuzeigen und zu bedienen.
Die Modernisierung beinhaltete die Integration der einzelnen Steuerungsteile in die vorhandene Steuerung sowie die Erweiterung des Visualisierungssystems zur Bedienung und Beobachtung der gesamten Linie. Dazu wurde die vorhandene Siemens- Steuerung durch eine moderne und leistungsstärkere Siemens-Steuerung mit modernen Schnittstellen ersetzt. Um die Sensorik der alten Steuerungen zu integrieren, wurde diese dezentral angebunden. Die vorhandenen „Hardware-Regler“ wurden durch „Software-Regler“ ersetzt. Für die Mehl- und Wasserdosierung wurde die vorhandene Dosierungssteuerung durch das Wiegemodul Siwarex FTC ersetzt.
Das bestehende PC-basierte Bedien- und Beobachtungssystem „InTouch“ wurde auf die neuste Version umgestellt und um die erneuerten Komponenten erweitert. Eine Rezepturverwaltung und Datenarchivierung runden die Bedienung der kompletten Linie ab.
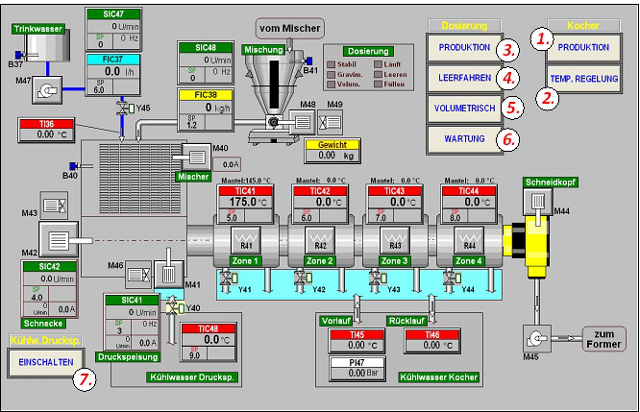
Prozessbeschreibung
Die Herstellung von Pellets erfolgt in mehreren Prozessstufen. Der hier beschriebene Anlagenteil (Linie 8) verarbeitet eine fertige Trockenmischung zu so genannten Pellets, die später zu dem fertigen Knabberprodukt weiterverarbeitet werden. Das Verwiegen und Zusammenstellen der Trockenmischung erfolgt in der zentralen Mischanlage und gelangt über ein Verbindungsrohr zur Linie.
Dort wird die ankommende Trockenmischung in einen Flügelmischer dosiert und mit Wasser befeuchtet. Eine Druckspeisung leitet die befeuchtete Mischung anschließend in einen Kochzylinder. Die eingespeiste Mischung wird über eine Schnecke durch mehrere Temperaturzonen zum Auslauf des Kochzylinders transportiert. Die Temperaturzonen im Koch-Zylinder sorgen dafür, dass die thermische Energie unter hohem Druck ins Produkt eingeleitet wird. Am Ende dieses Vorgangs wird die erhitzte Mischung durch Schneidmesser zerkleinert und über Gebläse zum nachfolgenden Former-Extruder transportiert.
Die zerkleinerten Teigstücke gelangen in einen Flügelmischer, an dessen Auslauf die Feuchtigkeit abgesaugt wird. Die Former- Schnecke nimmt den Teig auf und fördert diesen zum Auslauf des Zylinders. Je nach Produkt wird der Teig mit Hilfe von Schneid- und Malwerkzeugen in die geforderte Form und Farbe (Lebensmittelfarbe) gebracht. Fördergebläse transportieren den in Form gebrachten Teig in den Trocknerbereich der Linie. Die Trocknung besteht aus mehreren Stufen und bildet physikalisch den größten Platzanspruch der Linie. Nach der Trocknung entstehen aus dem geformten Teig die Pellets. Diese werden nach dem Trocknerbereich gekühlt und zur Endverpackung transportiert.
Die Steuerung
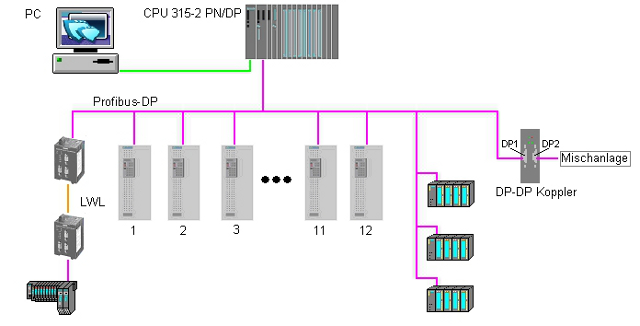
Die Visualisierung der kompletten Linie ist mit InTouch in der Version 10.1 realisiert. Die Anbindung zur Steuerung erfolgt über Ethernet. Als Steuerung kommt eine moderne S7-300 CPU (315-2 PN/DP) zum Einsatz. Über ein umfangreiches Profibusnetz sind die dezentralen Baugruppen und Frequenzumrichter mit der Steuerung verbunden.
Warum HIT?
HIT hat die Modernisierung einer Fertigungslinie für Schinkenchips mit Erfolg abgeschlossen. Den Bedienern wurde eine übersichtliche Bedienoberfläche gestaltet und für das Serviceteam eine gute Anlagen- und Softwarestruktur geschaffen. Von Beginn an hat die Anlage ihre Zuverlässigkeit bewiesen. Diese Eigenschaften erhöhen die Ausfallsicherheit und die Produktivität der Anlage.