HIT has automated three sections of a new glass wool facility. The three sections consist of an electronical equipment of the cullet water system, the flue gas scrubber system and the process water system.
The cullet water system
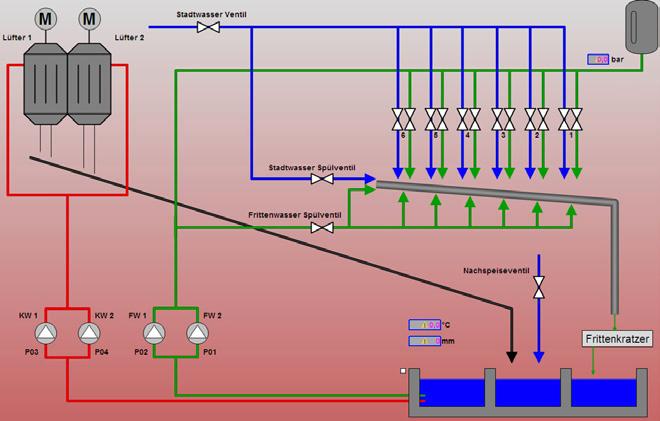
The cullet water system supplies the so-called ‘cullet channels’and the ‘rinsing channels’ with water. As long as a defibering machine does not produce glass fibres, but with the glass nozzles already open, the cullet channels with water running through them conduct the liquid glass to the cullet claws where the glass is cooled and separated from the water for further processing. The water is then conducted back into the cullet water collectors.
The main task of the cullet water system control is to maintain the water pressure in the pressure receptacle. Additionally, the water temperature and the level in the collectors is recorded and regulated. The cullet claws are also turned on/off and monitored using this system.
The flue gas scrubber system
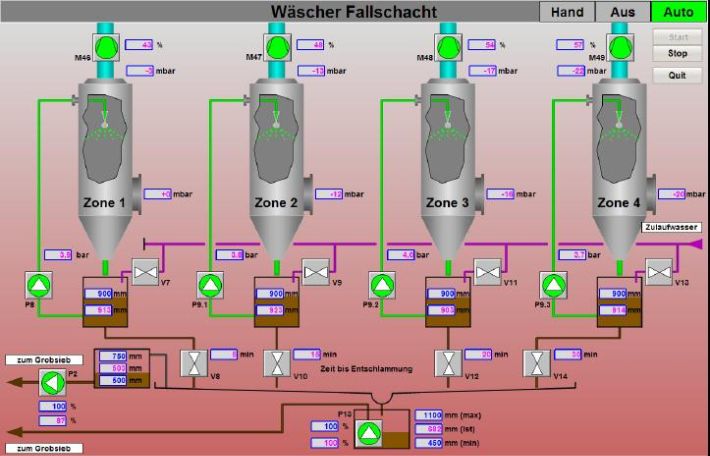
The facility includes 16 flue gas scrubbers in all, which in principle work in the same way. The system is divided into two units: a chute scrubber and an annealing oven scrubber. Both units are running separately from one another but are controlled by one CPU. The main task of the flue gas scrubber system is the cleaning of the polluted air. The exhaust fumes are sucked in by ventilators from bottom to top and conducted through lamellae. Water is sprayed on the lamellae from above at high pressure. This process cleans the air.
The process water system
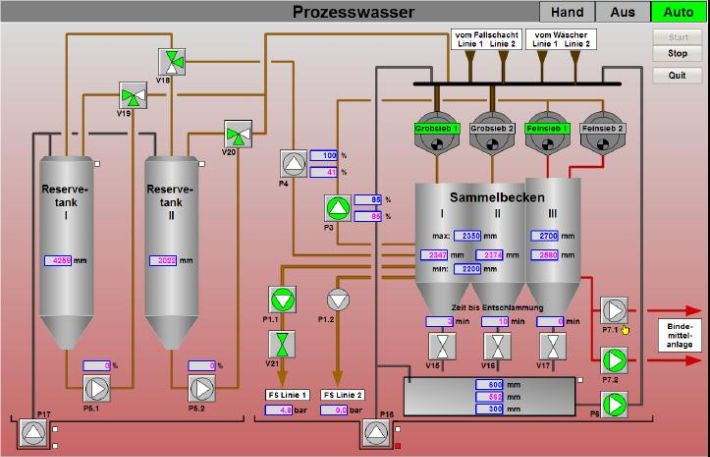
The process water system cleans the water of suspended solids and oil. The system has two coarse sieves and two fine-mesh sieves which filter the water. The cleaning process is so effective that no waste water leaves the system. The cleaned water is being fed back into the process afterwards.
The visualisation
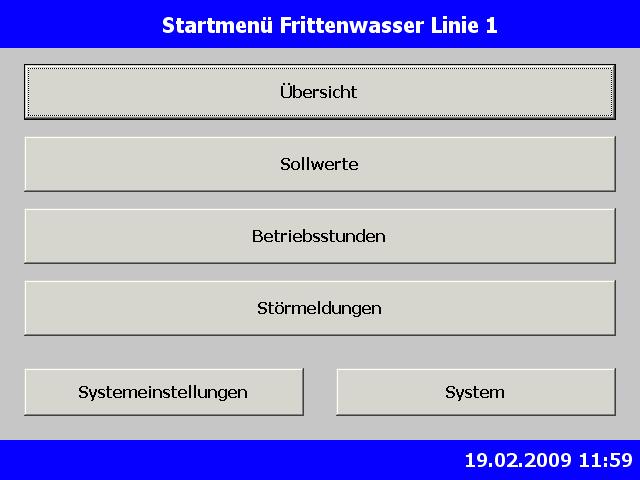
he visualisation of the systems is via panels or WinCC user interface. The target data and actual data display for pressure, temperature and fill level is designed in the same way. Additionally, the parameters can be adjusted on the WinCC user interface. The special feature of this system is the representation of all inputs and outputs of the PLC on the visualisation.
Why HIT?
HIT successfully completed this project. A clear user interface was designed for the operators and a good system and software structure was created for the service team. From the very beginning, the system proved its reliability. These features have increased the failsafe performance and the productivity of the system.